Type Rs are Honda racecars for the road so, a seam welded chassis is plausible, right? Here’s the truth.
For the longest time, you’ve probably heard the Acura Integra Type R has a seam welded chassis from the factory. It makes sense considering Honda is heavily influenced by their racing heritage, equip their cars with high-revving racecar-like engines, and even break long-held track records with these Type Rs.
And, going over some of the more popular Type R facts like hand ported engines and race-car like weight savings (no air conditioning and thinner floor mats,) it’s reasonable to expect Honda’s factory workers to crawl in and around the Integra Type R’s chassis, seam welding the spot-welded stock chassis for extra rigidity.
Seam welding, as the name says, is just that, a bunch of extra welding done the whole chassis through, focusing on key structural components like subframe bracing and shock towers. A stiffer chassis means a more efficient suspension system. And, if it costs only couple dollars of weld-material and time, it’s a no-brainer, right?
Here’s what the Acura Integra Type R Brochure says on Body/Structural enhancements. They mention a “stiffened body structure,” but don’t mention seam welding. Seam welding is a BIG enhancement to leave out if they actually did it.
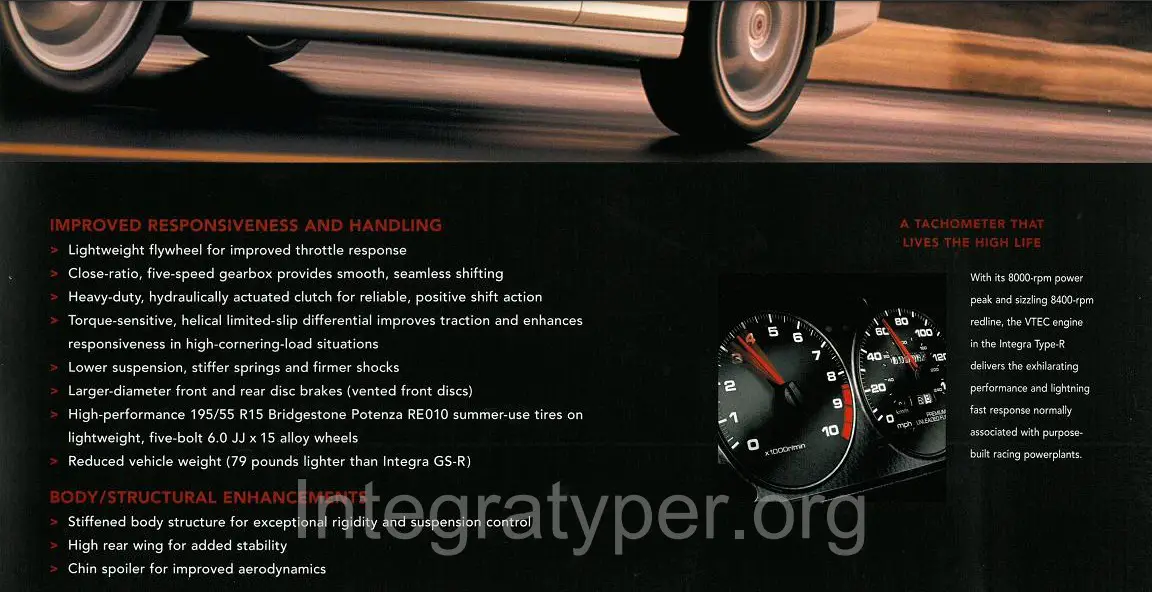
Let’s look at Acura’s technical information guide for the 1997 Acura Integra Type R, at 37-pages long, if there’s seam welding, this guide has to mention it.
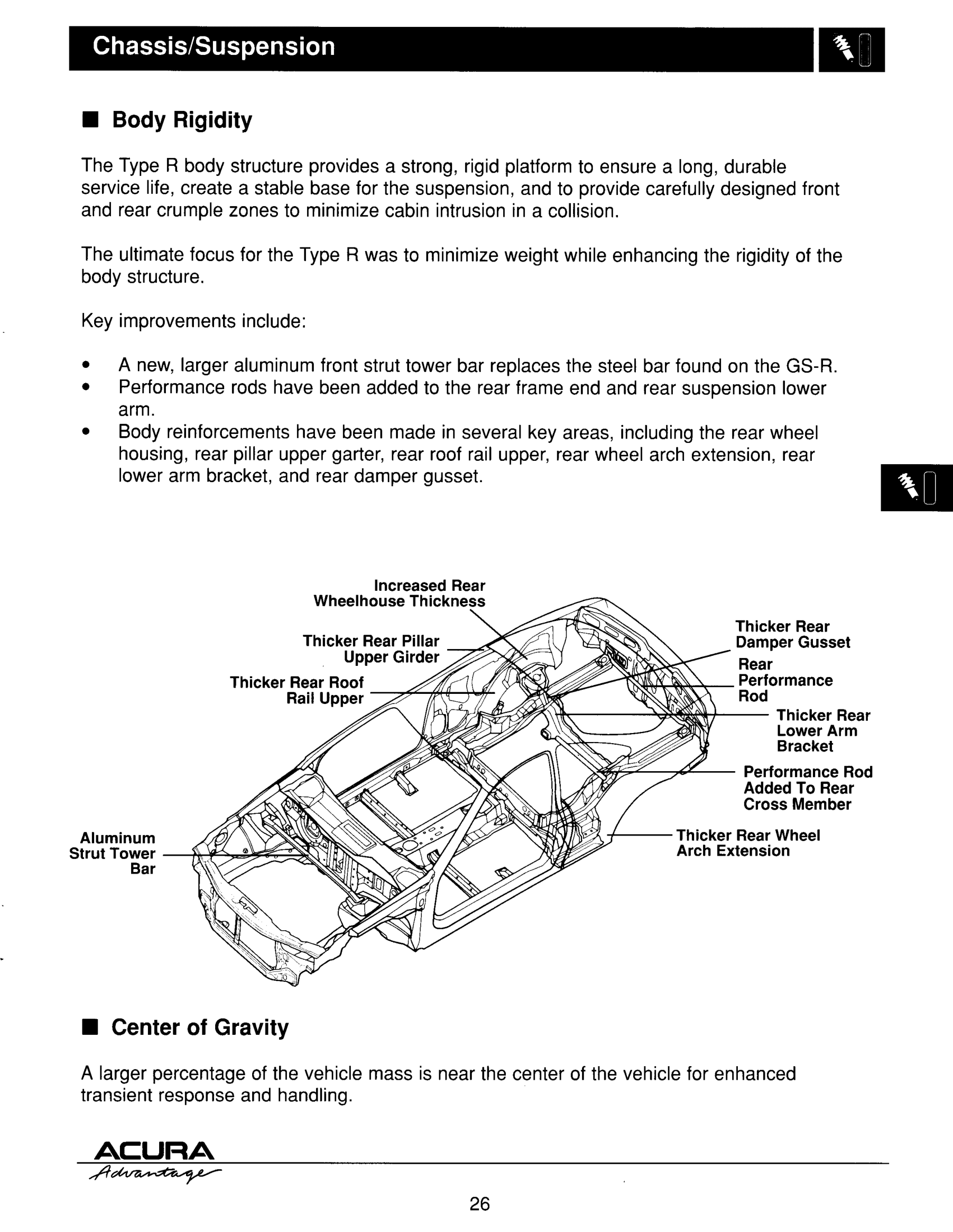
Again, this technical guide corroborates what the brochure says and expounds upon what they mean by “stiffened body structure.” You’ve got strut bars to stiffen up the front and rear suspension system, and thicker key areas in the rear to presumably help the Integra Type R rotate around corners.
But, no mention of seam welding.
Finally, let’s hear from Honda Chief engineer Shigeru Uehara specifically expounding on body improvements.
“Compared to the original model, various body parts have been improved with increased thickness,” says Uehara.
In addition, strut tower bars have been added to some spots, such as in the rear, a bar that ties the rear arms together and other performance rods.”
Again, no mention of seam welding.
The truth is the DC2 Acura Integra Type R does not have a seam welded chassis. While seam welding the chassis would’ve been cheap and would stiffen the Integra Type R, on a street car, it’s not safe.
Seam welding assumes your racecar already has other safety enhancements like a roll cage, fire suppression system, and you’ll be racing in a fire suit and helmet.
Seam welding means, in the event of a collision, stock body panels do not break and deform, absorbing energy, as designed. Instead, the strengthened chassis does not break apart in a collision and transfers that energy to its occupants. Seam welding is not practical for street-driven cars.
Honda’s chassis engineers determined that bars and thicker areas in the body were all that was needed to achieve performance goals. Seam welding would add negligible gains to an already stiff chassis.
TypeRClub.org member Wibbs puts it best.
“It’s my humble opinion that the seam welding claim is more to do with either an internet belief that caught on or some journalist reckoned it was, and it’s been repeated ever since,” Wibbs says.
“I’ve had my JDM R near down to the bare bones and didn’t see any evidence of seam welding. I’ve also been involved in stripping a UK/Euro spec Type R. I did see the extra metal around the rear strut turrets, and it had more spot welds in various places than a JDM SiR that I stripped for various panels, but no seam welds.“
“I have a few bits of Honda sales and promotional literature(JDM/UKDM/ITDM/OZDM) from the time and “chassis reinforcements” yes, but no mention of seam welding.“
That definitely puts that rumor to rest. The DC2 Integra Type R has a stiffened chassis, but engineers achieved that stiffness without resorting to seam welding.